無數次的嘗試與失敗,無數次的汗水與淚水交織,匯聚成了這條核電裝備自主化研制的道路。
廢寢忘食,工程師們沉浸在數據的海洋中,反復計算、模擬、優化,只為找到那個最完美的設計方案;挑燈夜戰,他們攻克了一個又一個技術難關,解決了材料選擇、結構設計、制造工藝等一系列難題。
2021年1月30日,“華龍一號”全球首堆——福清核電5號機組成功投入商業運行,成為全球唯一按計劃建成的三代核電。
“華龍一號”汽水分離再熱器冷試(MSR)、熱試、性能考核試驗均一次通過,商運性能高于保證值,全面驗證了東方電氣集團所屬東方重機過硬的設計技術,兌現了“超越客戶愿望”的承諾。
那一刻,整個辦公室沸騰了,所有的疲憊與困苦都在這一刻化為了無盡的喜悅與自豪。
負重前行,開啟自主設計之路
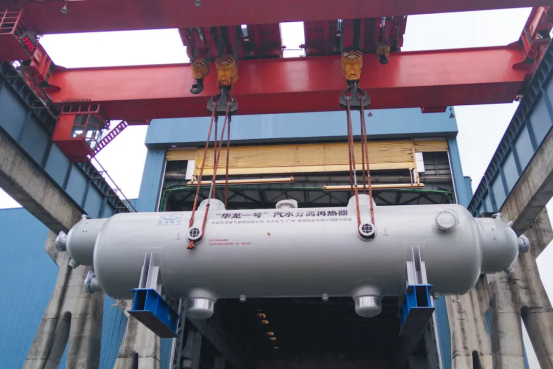
關于夢想與堅持、挑戰與突破的故事正在這里,悄然上演。
2005年,東方重機承接了國外核電汽水分離再熱器的技術轉讓,條款卻異常苛刻:核心技術被嚴密保護,高昂的技術服務費更是讓人望而卻步。
當時,MSR所有分離器組件、換熱管需要國外供貨,兩大關鍵核心技術受制,還要按照國外技術供方的要求,必須使用他們提供的專用軟件來完成設計工作,結構也不能有任何修改。
正是這些看似不可逾越的障礙,激發了東方電氣人的斗志和創造力。
“研發完全具有自主知識產權的核電主設備,是中國幾代核工業人的夢想。”李東銘博士作為MSR性能設計的負責人,帶領著一支充滿激情與智慧的團隊,踏上了這條充滿未知與艱辛的征途。
“我們必須打破國外技術封鎖,走自主化設計之路。”但是,作為國內首個研發承擔單位,研制的難度、風險和成本無疑是巨大的,“產品性能如何保證、技術領先如何實現、追趕計劃能否滿足進度要求,來自行業內的質疑不絕于耳。”
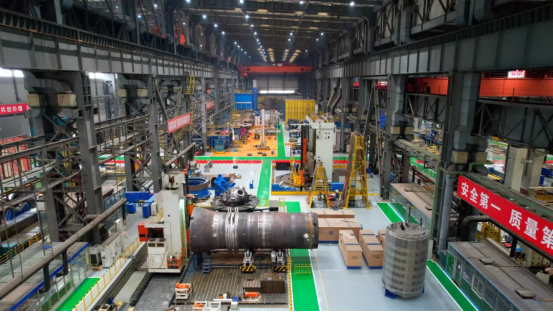
時間回溯到2010年的初夏,在中國機械聯合會的會議室里,一場關乎中國核電裝備自主化的匯報評審會正在緊張地進行著。會議桌上,各方專家匯聚一堂,討論的焦點如同夏日午后的一場“急雨”,激烈而緊迫——在面對汽水分離再熱器研發時,中國是應該選擇自己獨立研發,還是與國際大廠攜手合作?
空氣凝固了,各方都陷入了沉思。這時,一位身材干練的中年男子站了出來,他便是“華龍一號”汽水分離再熱器設計總師劉曉鴻。面對滿場的質疑與期待,劉曉鴻的聲音清晰而有力:“我們要完全自己設計!”
劉曉鴻深知,這條自主設計的道路將布滿荊棘,但他更清楚,只有掌握了核心技術,中國核電裝備才能真正實現自主可控。
這是一塊硬骨頭,但他愿意帶領團隊,義無反顧地啃下去。
迎難而上,占領核心技術高地
“波紋板和換熱管的設計是MSR設計最艱難的任務。”這意味著,在設計過程中,團隊必須小心翼翼地在既定框架內尋找創新的可能。
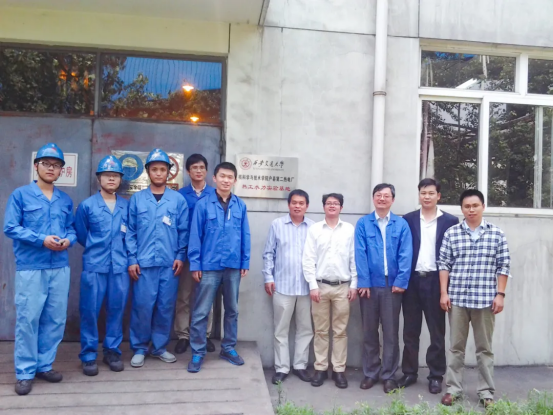
李東銘和團隊成員
李東銘博士和他的團隊夜以繼日地工作,對每一個細節進行反復推敲和驗證。“我們就從動量守恒方程直接推導出翅片間距設計公式,結合換熱機理,形成了該類型低肋高密度翅片換熱管設計方法。”
經過無數次的試驗和改進,團隊終于突破了技術瓶頸,開發出具有自主知識產權且比國外同類產品效率更高的新型換熱管。這個突破性創新為提升產品換熱性能及其國產化奠定了基礎。
紙上得來終覺淺,為確保設計方案在實際工程應用中的穩定性和可靠性,他們必須面對更為嚴峻的挑戰——用同參數蒸汽進行熱態性能驗證試驗。
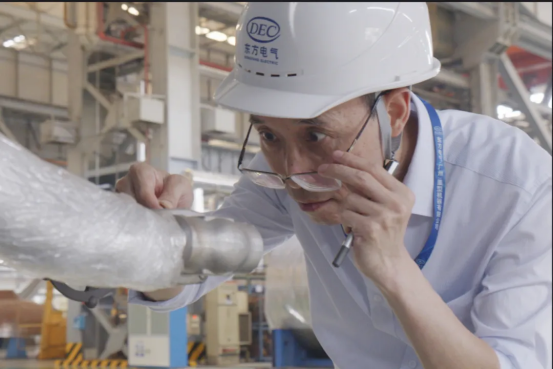
劉曉鴻正在分析試驗臺架問題
“新設計、新工藝、新設備必須進行大量的論證實驗。”劉曉鴻深知這一點的重要性。2011年開始,他便帶領著一支由技術精英組成的隊伍,踏上了尋找合適熱工試驗單位的征途。
他們跑遍了全國,每一個可能進行熱態性能驗證試驗的單位都留下了他們的足跡。在這個過程中,他們不僅要面對項目執行進度緊迫的壓力,還要克服科研課題等多方面的挑戰。“這是我們必須跨越的障礙,也是通往成功的必經之路。”
經過大半年的不懈努力,他們終于與兩家國內科研院所達成了合作意向。“那一陣子項目進度壓力非常大,科研、項目等各條線都催得緊急,沒日沒夜地全身心都撲在項目上,掉不得‘鏈子’。”
試驗方案的制定是第一步,也是最關鍵的一步。國內尚未有任何關于再熱器和分離器理論研究、分析計算和試驗研究的數據,完全處于一片空白地帶。
沒有現成的經驗可供借鑒,團隊只能依靠自己的專業知識和實踐經驗,不斷推翻舊的方案,又不斷重建新的方案。每一次的推翻都意味著他們需要重新審視問題、重新尋找答案,每一次的重建都凝聚著他們的智慧和汗水。
“前后共進行了30余次的技術評審及論證。”劉曉鴻對這個艱難的過程只是輕描淡寫地說著。
探索與創新的道路上,從來就沒有一帆風順的坦途:再熱器預試驗的結果與預期差異巨大,項目進度、成本壓力陡增。
這條路還走得通嗎?一時間團隊意見陷入了分歧。
“不破不立!我們沒有退路!”李東銘果斷地提出切開試驗件,查找是設計錯誤還是試驗問題。
在進行分離器試驗時,汽水混合物中水珠粒徑大小是影響分離性能最重要的因素,“可是,實際產品運行粒徑是多少?國內外沒有資料可循,國內也沒有相關測量手段,試驗又陷入了僵局。”
騎虎難下之時,劉曉鴻經過廣泛征求多方意見、深入研究,歷經半年理論論證和試驗臺架改造,制定出業內專家認可的試驗方案。
“我們做到了!”這句話在團隊每個人的心中回響,攻堅路上的艱辛與疲憊仿佛都煙消云散,取而代之的是難以言喻的喜悅與自豪,兩項試驗均取得預期效果,猶如給團隊打了一針“強心劑”,鼓足了他們繼續前行的信心。
4年時間,技術團隊成功研發出具有自主知識產權的MSR用高性能雙鉤波紋板及高密度新型換熱管,兩項技術博采眾長,處于國際領先地位。
巧妙設計,打破國外專利壁壘
“要有實實在在的自主,就必須打破國外知識產權壁壘,不然一切工作都白費了。”李東銘牽頭與結構負責人鄭煥比對標準、運行、維護等要求,逐一對大部件進行分解,建立屬于有自主知識產權的“華龍一號”MSR結構設計和設備啟停要求。
“我們從理論和試驗結果對MSR內部的部件逐一制定分析方法。”熱工負責人張玉禎從高溫高壓下的“流體物性”變化,到蒸汽流動路徑的微小偏差,每一個細節都逃不過她們的眼睛,成功建立一套MSR主蒸汽流場分析方案。
標準的制定與完善是提升產品質量的基石。工藝總負責人劉遠彬牽頭首次采用國家標準,結合生產制造經驗,填補了GB/T 151和NB/T 47014標準的相關空白。“我們補充了管子管板密封焊規定、優化了管板堆焊過渡層材料降低出現缺陷風險、固化了管板國標材料封口焊工藝,形成了一系列標準和規程。”這一系列標準和規程的制定與實施,為整個行業樹立了新的標桿。
看似尋常最奇崛,成如容易卻艱辛。
十年間,東方重機贏回了分離器采購權,降低了采購成本和制造周期;提升了出口蒸汽品質,自主設計的新型換熱管提升了蒸汽出口溫度,提高了產品整體性能;獲得了知識產權13項,軟件著作權1項。
十年,或許只是時間的推移與項目的推進,但背后的故事卻是無數次的技術攻關、無數次的試驗失敗與再嘗試,以及面對重重困難時那份堅定不移的信念與決心。
“是的,我們終于干成了這件事,當時山重水復疑無路,現在回過頭來看,這是我們拼過的證明!”劉曉鴻滿懷深情地望向遠方。
回首來時路,是為了邁向前方更遠的征程。